21.07.2021
Design for humanitarian emergencies – Jengu
Stephen Philips, MCSD Product Chartered Designer.
Associate Product Designer Arup.
Over the course of my journey as a product designer, I have always strived to create a better world, both for people and the planet, and I’m sure it’s the same for most designers. I also do it because aside from my family, design is what I am most passionate about. My journey so far has been both challenging and rewarding, with plenty of obstacles and occasional moments of sheer satisfaction when everything came good along the way.
In 2008, I joined the global design and engineering firm Arup. I knew the organisation was responsible for some of the most innovative and challenging projects in the built environment and it had (and still has) a reputation for employing some of the most skilled and talented engineers on the planet, including the likes of Cecil Balmond and Peter Rice who were able to plan and engineer materials, structures and buildings to realise some of the most gravity-defying and deft architectural visions on the planet.
At Arup, I relished the opportunity to collaborate with some amazing people and grow technically as a designer, but perhaps the most attractive thing was its core aim to ‘Shape a Better World’. The simple mission statement has real meaning, and the employee-owned organisation allows us to make decisions and organise ourselves to reach that lofty goal.
In 2018, we were approached by The British Red Cross with a weighty challenge. It was having problems finding effective handwashing hardware for humanitarian emergency situations. Such a project required a deep understanding of its problem and we engaged expertise from the British Red Cross and London School of Hygiene and Tropical Medicine to determine the most effective hygiene action to tackle this problem.
Product design in developing nations
In developing nations, gastrointestinal illnesses, such as diarrhoea, kill more than 1.5 million people every year, so this is a considerable problem. The conclusion was that handwashing with water and soap is one of the most critical actions people can take to stop prevent gastrointestinal illness and most recently, Covid19. Yet, in many parts of the developing world, people don’t have access to basic handwashing facilities. There is a general lack of durable and effective handwashing units available that are quick to deploy and appealing to use. There can be a lack of water infrastructure and when available, water can be scarce so particularly in this context it’s a precious resource.
As the designer, I needed to unpack the problem and because we were looking to change people’s behaviour around handwashing, I was joined from Arup by a psychologist, an international development specialist and specialists in water, sanitation and hygiene from the Red Cross. We carried out in depth research, visiting a refugee community in Uganda, talking about the problem with the refugee community from the Democratic Republic of the Congo, in the heart of Africa. They were clearly well-aware of sinks, basins and taps, also becoming well connected with changes in the rest of the world, with increasing access to media and mobile phones.
As a result of our research into the problem, we developed the ‘Jengu’ handwashing unit. Because most people globally subconsciously associate a basin- with a tap and soap – with handwashing, and we wanted the unit to incorporate a recognisable sink, with a faucet and area for bar soap and liquid soap. This was to provide familiarity and comfort for people in a stressful situation.
For robustness and ease of fabrication in different locations, we used steel. We designed the unit with four legs for stability, large feet to prevent it sinking into soft ground, and a shallow basin and compact faucet.
- Jengu frames fabricated from sheet and tubular steel. Image: Littlehampton Welding.
- Jengu frames fabricated from sheet and tubular steel. Image: Littlehampton Welding.
To supply and control the water, we used a soft rubber foot pump and reduced the amount of water supplied to ‘just enough’. This reduced the potential for hand contamination associated with taps and meant water was only supplied when needed. Wastewater could be drained by a hose into a soakaway or drain.
Liquid or bar soap could be secured to Jengu, and crucially, water could be supplied from a range of water tanks from 20 litre jerry cans to larger, more permanent tanks. Many handwashing units in this sphere rely on the supply of water through gravity, but this means the user must refill the tank above waist height which can be difficult. To make refilling of gravity tanks easier, many handwashing units are lower than they should be, making them uncomfortable for taller people to use.
With Jengu’s foot pump control, the water container could be on the ground, making it easy to refill and the basin remained at the correct height. We decided to provide Jengu in two heights, one for children and one for adults. A version for people with reduced mobility is in development. The Jengu unit had to incorporate a mirror, so we used mirrored stainless steel so it couldn’t get smashed or peel off. The mirror was to provide additional benefit to users and allow users to wash their face and eye’s also helping to reduce the prevalence of trachoma, a bacterial infection that is a leading cause of blindness.

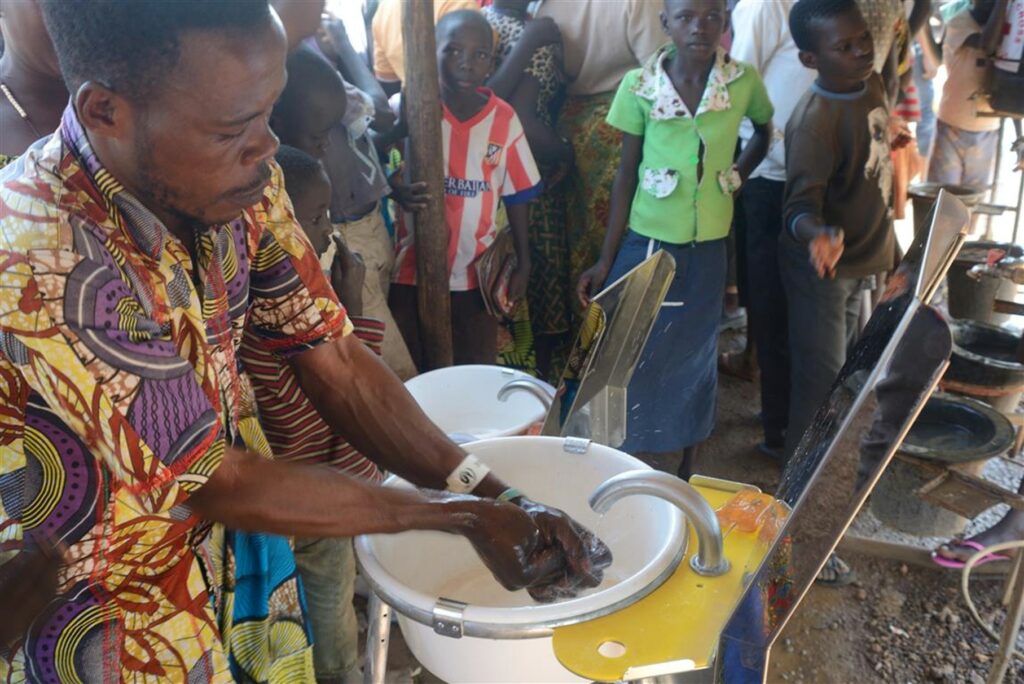
Jengu handwashing units. Image: Gregory Rose.
Testing and learning in product design
Prototypes were made and tested by the Royal Engineers and the British Red Cross. At the time, we also sent one prototype to Shenzhen Design Week as part of the Chartered Society of Designer’s London Pavilion showcase in 2019.
One request from the NGO community was for Jengu to be ‘open source’, so that anyone could use the design information to make the unit relatively locally to where it is needed. This is a different model to the usual manufacture and distribute system where products are manufactured and assembled in volume at a specialist factory in one location. Finished products shipped to agents and national distributors, where the last mile purchase and delivery happens. With Jengu, we had to identify manufacturers who could make the units in close proximity to where they would be deployed and the choice of fabricated steel, combined with readily available components such as washing up bowls and hose pipes, sourced locally allowed this. A valuable by-product of local manufacturing is that funding is invested in local enterprise, supporting the community with local jobs and training.
During the summer of 2020, when the UK came out of the first Covid19 lock-down, to reduce risk of viral transmission through handwashing with soap and water, a pilot production of 50 Jengu handwashing units were made by a fabricator in Plymouth and deployed across the UK, from Bristol to Newcastle. Thirty Jengu units went to schools, twelve to help the homeless organisations and eight to community organisations including a mountain rescue centre! Units were placed at the entrances to classrooms and schools, providing an instant handwashing solution without the need for plumbing. This was a great opportunity to get feedback as to what people thought of Jengu.
Children and adults alike found it a fun and worthwhile handwashing experience, reinforcing the need for effective hand hygiene to stay safe.
Recently, Save the Children was successful in securing funding to make and deploy 250 Jengu units in Kenya. We carried out a search for manufacturers with the capability to fabricate and assemble the units and source the fit on components locally in East Africa. The manufacturer completed the units allowing Save the Children to deploy the Jengu handwashing with soap and water in Nairobi’s informal settlements.
I hope the results of this fascinating project will help the vulnerable communities that need more effective handwashing hardware the most. It will also allow an appraisal of the open source design and production model, something I am still getting to grips with.
For more information on the Jengu project, visit https://jengu.org.uk/